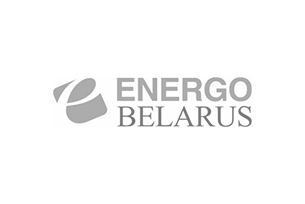
Энергетический переход: вызовы и возможности для России
19.08.2024
Применение термитной (экзотермической) сварки для соединения элементов заземляющих устройств в свете требований ГОСТ Р 50571.5.54-2013.
Соединения проводников представляют собой слабое место всех электросетей и, особенно цепей заземления, подверженных изменению свойств в результате коррозии и увеличения переходных сопротивлений. Вступивший с силу с 01.01.2015 года ГОСТ Р 50571.5.54-2013 / МЭК 60364-5-54:2011 «Электроустановки низковольтные. Часть 5-54. Выбор и монтаж электрооборудования. Заземляющие устройства, защитные проводники и защитные проводники уравнивания потенциалов» (далее ГОСТ) вносит изменения в способы соединения элементов заземлителей. А именно, пункт 542.2.8 гласит «Если заземлитель состоит из частей, которые должны быть соединены вместе, соединение должно быть выполнено экзотермической сваркой, опрессовкой, зажимами или другим разрешённым механическим соединителем». Чем же вызвано исключение электродуговой сварки из допустимых способов соединения?
Использование электродуговой сварки ввиду достаточно длительного воздействия (от десятков секунд до нескольких минут) высоких температур (свыше 700°С) на свариваемые металлы приводит не только к значительной потере цинкового и любого другого защитного слоя в районе сварного шва, но и существенно ослабляет коррозионную стойкость свариваемых металлов, вызывая межкристаллитную коррозию (Рис.1). Это вид коррозии, при котором разрушение металла происходит преимущественно вдоль границ зёрен (кристаллов).
Рисунок 1. Микроструктура материала, подверженного межкристаллитной коррозии
При малой коррозионной потере массы разрушение материала может проникать на большую глубину и сопровождаться снижением механической прочности материала, изменением его свойств, в том числе электрической проводимости. Межкристаллитная коррозия относится к электрохимическим процессам, и обусловлена тем, что твердый раствор при определенных условиях может расслаиваться с образованием по границам зерен фаз, обогащенных одним из компонентов материала, а участки, непосредственно прилегающие к границам зерен, оказываются обедненными этим компонентом. Под действием той или иной агрессивной среды происходит избирательное анодное растворение либо обогащенных, либо соседних с ними обедненных зон.
Одной из основных причин разделения фаз является нагрев металлов на долгое время свыше 700°C.
Вероятно, появление межкристаллитной коррозии в местах сварных соединений и послужило одной из причин исключения электродуговой сварки как способа соединения элементов заземлителя между собой.
Ещё одним способом соединения частей заземлителей, который предлагает нам ГОСТ, являются болтовые зажимы, которые относятся к разрешённым механическим соединителям (Рис.2). Применение зажимов должно обеспечивать требования ГОСТ 10434 «Соединения контактные электрические. Общие технические требования» ко 2-му классу соединений. Соединения должны быть защищены от коррозии и механических повреждений. Для болтовых соединений должны быть предусмотрены меры против ослабления контакта.
Рисунок 2. Вариант применения болтового зажима для соединения элементов заземлителя
При всей простоте и удобстве использования данного вида соединений, они имеют ряд недостатков. Во-первых, применение механических зажимов, по сравнению со сварными соединениями, для соединения частей заземлителя увеличивает переходные сопротивления, что в свою очередь может привести к превышению нормируемого значения сопротивления ЗУ. Во-вторых, механические зажимы требуют периодического контроля места соединения, что влечёт дополнительные затраты на обеспечение доступа к соединениям, например, использование инспекционных колодцев, и их обслуживание.
Практически, те же недостатки присущи и соединениям выполненным опрессовкой.
Наиболее эффективным способом соединения элементов заземляющих устройств представляется термитная (экзотермическая) сварка в соответствии с требованиями п. 542.2.8 вышеуказанного ГОСТ.
Термитная сварка — процесс сварки металлических деталей жидким металлом заданного химического состава, получаемого в результате термитной (алюминотермической) реакции. Сущность термитной реакции заключается в том, что алюминий способен восстанавливать окислы металлов со значительным выделением тепла, в результате чего происходит изменение потенциального состояния энергии и рекристаллизация компонентов, участвующих в процессе.
Способ соединения с помощью термитной сварки обеспечивает возможность создания связей на молекулярном уровне при соединении различных металлов в любых комбинациях (медь, латунь, бронза, сталь, в том числе оцинкованная, омеднённая и нержавеющая) без каких либо внешних источников энергии и тепла (Рис3).
Рисунок 3. Пример использования термитной сварки для соединения проводников
Принцип термитной сварки основан на использовании термитной смеси, состоящей из окислителей и восстановителей, которые при определённой температуре вступают друг с другом в реакцию с выделением большого количества тепла.
Чтобы осуществить термохимическую реакцию между восстановителем и окислителем, необходимо наличие определенных условий, как то: химической чистоты компонентов термитной смеси, соответствующего измельчения их, определенного соотношения составляющих термита в смеси, доведения термитной смеси до температуры начала реакции. Химическая чистота восстановителя и окислителя необходима для обеспечения определенной активности и теплотворной способности термита, а также для качества сварки. Для начала термитной реакции в любой точке термитной смеси необходимо создать температурный толчок около 1000°С, после чего термитная реакция быстро распространится на всю смесь. Для прохождения реакции горения нет необходимости в дополнительном атмосферном кислороде, т.к. он в достаточном количестве выделяется окислителем.
В настоящее время технология производства термитной сварки отвечает самым высоким требованиям по безопасности. Так, для поджига термитной смеси уже не применяются термитные спички. Данный способ сложно назвать безопасным, поскольку рука человека в момент поджига находится в непосредственной близости от поджигаемой термитной смеси. В настоящее время поджиг осуществляется с помощью дистанционного блока управления с кабелем длиной до 4 метров, что в принципе исключает возможность попадания капель расплавленного металла на человека. Термитная смесь в заводских условиях расфасована в герметичные металлические капсулы, что предотвращает попадание в неё влаги при транспортировке и подготовке к сварке и исключает вероятность взрыва при его поджиге.
Реакция происходит в верхней камере специальной жаростойкой формы (для каждого типа соединения предусмотрена своя форма). В результате реакции образуется сплав с температурой около 2000°С, который стекает в сварочную полость и, застывая на проводниках образует надёжное соединение на молекулярном уровне.
Порядок выполнения термитной сварки на примере «Т-образного» соединения полосовой стали 4х40 мм представлен на рисунке 4.
Рисунок 4. Порядок выполнения термитной сварки
1. На тигельной графитовой форме закрепляется ручной держатель формы для последующей фиксации свариваемых проводников.
2. Перед первым использованием после хранения поверхность формы прогревается с помощью газовой горелки для удаления влаги из графита. Данная процедура позволит избежать возможных выбросов металла из формы в ходе реакции.
3. В форму, аккуратно, чтобы избежать сколов графита, помещаются и фиксируются свариваемые проводники. При необходимости, для фиксации проводников применяется струбцина.
4. В форму устанавливается капсула с термитной смесью. Закрывается крышка формы.
5. К контактной пластине термитной капсулы подключается клемма блока управления дистанционным поджигом.
6. Нажатием кнопки на блоке управления инициируется процесс горения. Длительность реакции не превышает 1,5-2 сек.
7. После остывания формы (2-3 минуты) с помощью ручного держателя форма раскрывается и снимается с проводников. Внутренние полости формы очищаются от остатков металла и окалины с помощью скребка и кисточки.
8. Осуществляется осмотр произведённого соединения и проверка на качество сварки. Должны быть исключены непровар, прожог проводников, значительные шлаковые включения в сварной шов. Допускается незначительная пористость сварного шва. Надёжность сварки проверяется ударом молотка.
9. Место сварного соединения изолируется с помощью гидроизоляционной ленты. Образцы сварных соединений, сделанных с помощью термитной сварки, и их разрезы представлены на рисунке 5.
Рисунок 5. Образцы сварных соединений и их разрезы
Кроме того, в первом случае было выполнено соединение разнородных материалов, а именно, медного кабеля и пластины из нержавеющей стали.
На рисунке 6 представлен образец стыкового соединения стальной полосы с горячеоцинкованным покрытием. И, как мы видим, в результате сварки защитный цинковый слой в районе сварного шва не был разрушен.
Рисунок 6. Образец сварного соединения встык стальной полосы с горячеоцинкованным покрытием
Предпочтительность термитной сварки для соединения элементов заземляющих устройств обусловлена повышенной механической и коррозионной прочностью, как самого сварного соединения, так и свариваемого металла, вследствие более кратковременного воздействия высоких температур на свариваемые металлы. При сваривании достаточно тонких слоев материала металл не успевает прогреться до температур, ведущих к межкристаллитной коррозии. Шов сварного соединения имеет более высокую температуру плавления, чем свариваемые металлы, поэтому выдерживает бόльшие нагрузки по току. Применение термитной сварки для соединения элементов заземлителей обеспечивает механическую и коррозионную прочность сварных соединений ЗУ на весь срок службы оборудования.
Кроме того, термитная сварка отличается следующими преимуществами:
— удобство, малый вес и хорошая манёвренность используемой оснастки;
— возможность проводить сварку без дополнительных источников тепла и электроэнергии;
— высокая производительность;
— достаточные прочностные характеристики сварных соединений.
Процесс производства термитной сварки за счёт его технологичности достаточно прост и позволяет свести к минимуму влияние человеческого фактора на качество выполнения сварки. При производстве термитной сварки однотипных соединений используется типовой технологический процесс, типовое оборудование и материалы, что позволяет выполнять типовые соединения практически не отличающиеся по своему качеству друг от друга.
Для соединения элементов заземляющих устройств предлагается три типа форм (Таблица 1).
Таблица 1.
Внешний вид соединения |
Тип соединения |
![]() |
Соединение заземляющего электрода стального горячеоцинкованного d=16 мм с полосой стальной горячеоцинкованной сечением 4х40 мм |
![]() |
Соединение полосы стальной горячеоцинкованной сечением 4х40 мм «стык в стык» |
![]() |
«Т-образное» соединение полосы стальной горячеоцинкованной сечением 4х40 мм |
Как показывает практика, указанных типов соединений достаточно, чтобы произвести монтаж заземляющего устройства практически любой конфигурации.
Компания «Хакель Рос» поставляет комплекты термитной сварки как в составе Устройств заземляющих комплектных УЗК так и отдельно. Комплекты оснащаются необходимым количеством форм, термитов, держателей и прочей оснастки для их монтажа (Рис.5). В комплект входит технологическая карта производства сварки.
По требованию заказчика, компания может поставить необходимые формы и прочую оснастку под любые типы соединений проводников между собой круглого и плоского сечения различных размеров, а также проводников круглого и плоского сечения различных размеров к стальным поверхностям (швеллер, уголок и пр.) и арматуре.
Рисунок 7. Пример комплектации оборудованием и оснасткой комплекта термитной сварки.
Старший менеджер проекта ЗАО «Хакель Рос» Носков C.В.
Беларусь 29.10.2024
Тема дня 29.10.2024
Новости компаний 28.10.2024
Тема дня 26.10.2024
Тема дня 18.10.2024
Традиционная энергетика 03.05.2023