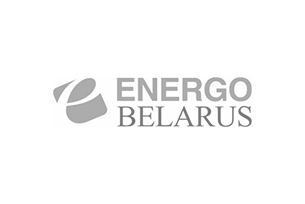
Готовое решение: солнечные электростанции на базе инверторов серии ECO
20.07.2021
Создание новых образцов техники, способных вовлекать в оборот местные энергоресурсы весьма актуально. Мотивация этого направления во многом объясняется устойчивым ростом цен на газ и нефть. Поэтому во всем мире ведется интенсивный поиск альтернативных энергоресурсов.
С конкретной разработкой установки локального энергообеспечения участников VII научно-технической конференции «Проблемы использования альтернативных видов топлива в строительном комплексе Республики Беларусь» ознакомил Геннадий Иванович Журавский – доктор технических наук, профессор, заведующий отделением ГНУ «Институт тепло- и массообмена им.А.В. Лыкова» НАН Беларуси.
В связи с устойчивым ростом цен на газ и нефть, во всем мире ведется интенсивный поиск альтернативных энергоресурсов. Одним из потенциальных источников такого вида энергии представляется энергия, выделяемая при сгорании биомассы (древесина, отходы производства и переработки сельскохозяйственной продукции, быстрорастущие лесные культуры) и горючих технологических отходов. Поэтому разработка и выпуск новых образцов техники, способных вовлекать в оборот местные энергоресурсы с целью замещения импортируемых, весьма актуальна.
Получение электроэнергии в данной цепочке преобразований является завершающим звеном, что наделяет разрабатываемую технику исключительными потребительскими достоинствами. Однако, как показал анализ проблемы, существующие технологии переработки биомассы и горючих технологических отходов с целью получения топлива значительно устарели и не отвечают современным требованиям по экологическим, экономическим и техническим показателям. В связи с этим, в ряде стран мира (Канада. Россия, США, Германия, Финляндия, Швеция и др.) приняты государственные программы по разработке высокоэффективных технологий производства топлива из биомассы и горючих органических отходов.
Одним из перспективных направлений создания таких технологий представляется получение горючих газов из биомассы и горючих органических отходов с последующим их использованием в когенерационных установках для получения тепловой и электрической энергии.
В начале XX столетия газификация угля, торфа и древесины являлась одним из основных методов производства горючего газа. Газификация осуществлялась в специальных аппаратах, называемых конверторами, реакторами, газогенераторами или газификаторами. Получаемый горючий газ часто содержал значительные количества твердых частиц и поэтому непосредственно мог быть использован только в котельных, обжигательных печах и других топках и только после охлаждения, очистки и сушки в качестве топлива в двигателях внутреннего сгорания.
Наиболее широкое промышленное развитие газификация получила к началу 60-х годов прошлого столетия. Однако вследствие быстрого роста добычи природного газа, развития сети газоснабжения и ужесточения требований к охране окружающей среды газификацию практически перестали применять. В последнее время в связи с необходимостью экономии тех или иных видов углеводородного топлива возрос интерес к горючим газам на основе биомассы и горючих органических отходов. Газ может быть получен путем газификации различных видов биомассы и горючих органических отходов:
- органических бытовых отходов, в том числе бумаги, резины,травы;
- отходов лесозаготовки и деревопереработ-ки, в том числе коры, обрезков деревьев, щепы, опилок и древесного угля;
- сельскохозяйственных отходов, в том числе соломы злаковых культур и рапса, стеблей кукурузы, льняных отходов, рисовой шелухи, скорлупы орехов и др.
При этом полученный газ обладает удельной теплотой сгорания от 4 до 20 МДж/м3 (теплота сгорания природного газа 33-36 МДж/м3). В условиях значительного повышения цен на жидкое топливо и природный газ особое значение приобретает возможность их замещения газом, получаемого из биомассы и горючих технологических отходов. Одной из таких возможностей является использование генераторного газа для производства тепла и электроэнергии малыми автономными когенерационными установками, роль которых в развитии локального энергообеспечения предприятий и индивидуальных потребителей в ближайшие годы будет возрастать.
Новизна разработки заключается в создании двухзонного газогенераторного модуля обращенного процесса горения, имеющего возможность термохимической переработки многокомпонентного сырья с целью снижения концентрации сернистых соединений в получаемом газе за счет их хе-мосорбции с компонентами золы топлива (СаО + S02 + 0,5О2 -> CaS04), повышения теплоты сгорания вырабатываемого газа и снижения вредных выбросов в окружающую атмосферу по сравнению с известными твердотопливными котлами.
Отличительной особенностью разработки является конструкция газогенератора, которая обеспечивает возможность совместной газификации твердых и жидких отходов, в том числе древесины, рапсовой соломы и тяжелых остатков нефтепродуктов и смол. Горючие растительные отходы в виде пеллет, брикетов или в измельченном виде будут подаваться в газогенератор в автоматическом режиме. Повышение тепловой эффективности газогенераторного модуля (КПД до 90 %) будет обеспечено за счет предварительного подогрева воздушного дутья и использования тепла отработавшей парогазовой смеси. Необходимый ресурс работы и экологичность установки будут обеспечены многоступенчатой системой очистки газа и продуктов его сгорания. Использование двигателя внутреннего сгорания позволит расширить область применения агрегатов, так как их эксплуатация в силу безопасности (в отличие от паро- и газотурбинных установок) будет доступна более широкому кругу пользователей.
Дополнительное тепло от охлаждения генераторного газа в теплообменнике агрегата может использоваться для отопления (водяное или воздушное) или на технологические нужды. Тепловая эффективность газогенератора, КПД которого на 6 % выше, чем у прототипа, определяется возвратом обратно в топочную зону части тепла от нагретых отработавших газов и снижения тепловых потерь при их последующей транспортировке в охлажденном виде. Повышение калорийности получаемого газа (выше, чем у лучших известных аналогов) обеспечено совместной газификацией твердых и жидких отходов, в том числе соломы, древесной щепы и опилок, мазута, смол и других отходов в измельченном виде или при их предварительном брикетировании, а также более полном термохимическом разложением отходов на легкие горючие компоненты в двух-зонной топочной камере.
Оборудование позволит получать генераторный газ с теплотой сгорания не менее 6,3 МДж/м3 и жаропроизводительностью до 2000 °С (у природного газа жаропроизводительность достигает 2050 °С). По удельному расходу топлива разработка соответствует лучшим мировым образцам техники. Данный газоэлектротеплогенератор будет обладать большей рентабельностью, чем известные аналоги, вследствие удешевления его изготовления за счет замены дорогих коррозионностойких сталей на черные с относительно недорогими защитными покрытиями.
Экономическая эффективность технологии и оборудования определяется экономией топливных ресурсов.
При эксплуатации оборудования для газификации древесных отходов с расходом Мт = 0,33 кг/с и теплотой сгорания гт = 10200 кДж/кг получается генераторный газ с расходом Gr = 0,6 м3/с и теплотой сгорания г. = 4175 кДж/м3 при нормальных условиях. Эффективность базового варианта оборудования составляет: к. п. д. = Gr-rr / (Мт-гт) = 0,6-4175 / /(0,33 10 200) = 71 %.
Затраты топлива при этом составляют: 0,33 кг/0,6 м3 =
При установке рекуперирующего теплообменника обратно через подогрев воздуха в камеру газификации можно возвратить тепло выходящих из газификатора генераторных газов в количестве:
N = cGr(tBx-tBbix) = 504KBT, (1)
где с = 1,4 кДж/(м3-град) - теплоемкость генераторного газа;
Gr = 0,6 м3/с - расход газа;
tBX = 720 °С - температура газа на входе в рекуператор;
tBbix = 120 °С - температура газа на выходе из рекуператора.
Эффективность базового варианта оборудования с рекуператором повысится до к. п. д. = Gr-r/(MT-rT- N) = 83 %. При этом для получения газа с таким же расходом потребуется топлива Мтр = (Мт-гт -N)/rT fa (0,33-10200 - 504) / / 10200 = 0,28 кг/с.
Затраты топлива составят 0,28 кг/0,6 м3 = 0,47 кг/м3 = 11,8-105 кг/кДж.
В качестве топлива может использовать смесь отходов древесины (соломы и т. п.) с отходами нефтепродуктов (отработанные масла, мазут). Смесь топлива, состоящая из 85 древесины и 15 % углеводородных отходов с теплотой сгорания 35 700 кДж/кг будет иметь общую теплоту сгорания гт = 14000 кДж/кг = 0,48-103 ту.т./кг. Из нее получится генераторный газ с выходом 1,8 м3/кг и теплотворной способностью 6300 кДж/м3.
Эффективность разрабатываемого оборудования составит:
- без рекуперации: к. п. д. = 1,8 • 6300 /14 000 = = 81 %, затраты топлива будут 1 кг/1,8 м3 = = 0,56 кг/м3 газа = 8,8-105 кг/кДж;
- с рекуперацией: к. п. д. = 1,8 • 6300 (14000 -- 1460) = 90 %, причем расход топлива будет М = 0,33 • 14 000 - 504 / 14 000 = 0,30 кг/с.
Удельные затраты топлива составят 0,30 кг/0,6 м3 = 0,5 кг/м3 газа = 7,9-105 кг/кДж производимого тепла. В целом экономичность разрабатываемого оборудования по сравнению с базовым по топливу составит
(14-10"5 - 7,9-Ю-5) / 14-Ю-5 = 43 %.
При выработке электроэнергии от электрогенератора с к.п.д. 80 % на окончательном этапе, подключенного к двигателю внутреннего сгорания с к. п. д. 30 %, вырабатываемая электроэнергия составит 0,8 • 0,3 » 24 % от полученной тепловой энергии от сжигания генераторного газа в двигателе, то есть для выработки электроэнергии мощностью 1 кВт необходимо затратить 1/0,24 = 4,2 кВт тепловой мощности от сжигания в двигателе генераторного газа или топлива в газогенераторе с расходом 4,2 кВт-7,9-10-5 кг/кДж = 0,33-103 кг/с. Для электрогенератора мощностью 100 кВт необходим двигатель внутреннего сгорания мощностью 140 кВт и газогенератор с теплопроизводительностью по вырабатываемому газу 400 кВт с расходом реального многокомпозитного топлива до 0,03 кг/с.
На 400 кВт полученной тепловой мощности и электрической до 100 кВт за один год при трехсменной работе и коэффициенте годовой загрузки, равном 0,5, у пользователя будет израсходовано топлива в виде местных отходов 500 т/год, что заместит импортируемые топливные ресурсы в эквиваленте 600 т у.т./год. Так как 1 т у.т. энергетически эквивалентна
При цене агрегата с тепловой мощностью в 400 кВт до 100 000 USD и эксплуатационных расходах до 2000 USD в месяц затраты пользователя окупятся менее чем за один год при использовании собственных отходов.
Маркетинговые исследования показывают, что основным потребителем новой техники могут являться предприятия промышленности строительных материалов, сельского хозяйства и жилищно-коммунального хозяйства, а также потребители, удаленные от централизованных систем энергообеспечения.
На состоявшейся конференции была представлена схема опытного образца газогенератора, разработанного для получения тепловой энергии, приспособленного для работы на топливе, представляющем собой смесь горючих производственных отходов нефиксированного состава. К ним, в частности, относится обтирочный материал, загрязненный нефтепродуктами, отходы пластика разных видов, в том числе пленочного полиэтилена и пропилена, отходы лакокрасочных средств, древесные отходы, картонно-бумажные упаковочные отходы, кухонно-пищевые отходы, отходы горюче-смазочных материалов и др.
Этот газогенератор имеет тепловую мощность 200 кВт и габариты (без бойлера с водой, не показанного на рисунке) длиной
Генераторный газ из камеры газификации подается на дожигание в жаровую трубу. Подача первичного и вторичного воздуха регулируется соответствующими двумя заслонками. Рабочий объем исходной топливной смеси содержится в бункере. Негорючая минеральная фракция и зола накапливаются в зольнике под колосниковой решеткой. Дверца служит для периодической очистки зольника. Первичный розжиг генератора осуществляется через горловину с дверцей. Герметично прилегающая крышка бункера выполняет также функцию взрывного клапана. Горячие продукты сгорания, выходящие из жаровой трубы, подаются в теплообменник бойлера с водой для накопления и последующего потребления тепловой энергии. Габариты бойлера: длина
Новости компаний 16.07.2025
Новости компаний 15.07.2025
Новости компаний 09.07.2025
Новости компаний 09.06.2025
Новости компаний 07.04.2025
Технологии 17.06.2025
Традиционная энергетика 09.06.2025
Чтобы оставить комментарий или выставить рейтинг, нужно Войти или Зарегистрироваться
Читайте также