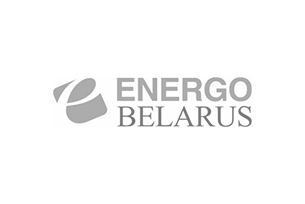
Коммутаторы Kyland для энергетики. Решения для автоматизации энергосистем
17.06.2025
После переработки товарного растительного сырья остается масса отходов, таких как опилки, кусковая древесина, кустарник, вершинник, различная солома от различных сельхозкультур, мезга льна, зерновая мякина, лузга подсолнечника и т.п. Это сырье может быть переработано в высококалорийное облагороженное топливо. Для этого исходную массу необходимо измельчить до размеров 2-5 мм, высушить до влажности 8-12% и для компактного вида спрессовать. Брикетный рукав, выходящий из экструдерного пресса, необходимо нарезать по требуемой длине. Полученное топливо имеет сравнительно высокую теплотворную способность, удобно в транспортировке, имеет сравнительно низкий зольный остаток.
Таким образом, из растительных отходов можно получить отличное и востребованное топливо. На выходе линий по переработке отходов могут быть гранулы или брикеты. Брикеты в свою очередь могут быть получены механическим или экструдерным прессованием.
В большинстве ведущих европейских стран мало или просто нет законов, написанных для топлива, полученного прессованием измельченных растительных отходов в виде гранул (пелет) или брикетов. Только в трех странах Австрии, Швеции, Германии введены специальные стандарты для топлива из биомассы. Другие страны со значительным оборотом прессованной биомассы, такие как Дания и Финляндия, предпочитают ожидать принятия общих европейских стандартов.
В отчете европейской комиссии CEN/TC 14961 даны предложения по принятию европейских стандартов на этот вид топлива.
Для иллюстрации свойств по теплотворной способности приводится сравнительная таблица удельной теплотворной способности распространѐнных видов топлива.
Вещество, топливо |
МДж/кг |
Ккал/кг |
Дрова сухие |
6 – 11 |
2000 – 2500 |
Каменный уголь |
27 |
6500 |
Торф |
10,5 – 15,5 |
2500 – 3500 |
Сланцы горючие |
7,5 – 15 |
1800 – 3600 |
Уголь подмосковный |
10,5 |
2500 |
Брикеты топливные |
16-20 |
4000-4700 |
Повышенное содержание коры не влияет на технологию шнекового брикетирования. Однако в коре – повышенное содержание зольного остатка.
В таблице 1 приводятся результаты измерения зольности для некоторых древесных материалов. Эти измерения выполнены в исследовательской лаборатории ПРУП «Усяж» Белорусского концерна по топливу и газификации.
Таблица 1
Результаты измерения зольности древесных материалов
Древесный материал
|
Зольный остаток %
|
Кора берѐзы
|
2.2
|
Кора сосны
|
2.1
|
Хвоя сосны
|
2.5
|
Хвоя ели
|
5.3
|
Листья кустарника
|
7,3 |
Кора молодых веток
|
6,3 |
|
В настоящее время рынок по реализации брикетов стремительно растет. Цены тоже непрерывно повышаются, особенно после подписания Киотского протокола. Преимущества этого вида топлива очевидны, и спрос на него будет только расти.
Брикеты, полученные шнековым прессованием, имеют в сечении форму 4-х или 8-ми многоугольника. Диаметр описанной окружности может быть 60-80 мм. В середине брикета выполняется отверстие диаметром 18-22 мм. Это отверстие при прессовании способствует получению монолитного рукава и при сжигании увеличивает площадь горения. Длина брикета определяется пожеланием заказчика или иной целесообразностью.
Область применения брикетов – все виды отопительного оборудования, работающего на твѐрдом топливе (отопительные котлы, печи, камины и т.п.). Например, для зимних условий средней полосы для эффективного отопления дома площадью около 250 м2 в сутки достаточно использовать не более 35 кг брикетов, то есть при длине 230 мм около 42 штук.
Существует мнение, что невозможна автоматизация процесса загрузки брикетов в топку. Если резку рукава производить по длине 60-70 мм, то загрузку в топку может производить любое шнековое устройство с диаметром от 250 мм. Такие устройства широко представлены на промышленном рынке.
Брикеты, полученные на экструдерном прессе, имеют наибольшую цену на европейском и внутреннем рынках. Ниже приводится краткая справка по технологическим операциям при производстве топливных брикетов.
1. Измельчение растительных отходов
Как ни странно, этот процесс наименее реализован применительно к процессу шнекового прессования. Древесные отходы должны быть измельчены до фракции 1-3 мм. На практике этот процесс реализуется двумя агрегатами: дисковая резка, которая перерабатывает отходы в щепу и дальнейшее доизмельчение до необходимой фракции. Сочетать эти операции в одном агрегате пока не удаѐтся. Нет хорошо работающих аппаратов для измельчения щепы.
Измельчение соломы до фракции не более 5 мм пока также окончательно не решѐнная задача. При измельчении мезги льна возникает проблема с длинными волокнами, которые могут наматываться на вращающиеся части.
2. Процесс сушки
Процесс шнекового прессования успешно может идти при влажности растительных материалов от 6 до 14%. Европейские стандарты требуют влажности полученного брикета не более 12%.
Наиболее распространена сушка растительных масс в сушильных барабанах при прямом воздействии топочных газов на сырьѐ, подлежащий сушке (прямой нагрев). Температура дымовых газов (пламя горящего дизельного топлива или топочные газы) может достигать 400-600 0С. Такая высокая температура даѐт высокий потенциал для процесса сушки. Однако, применение такого метода имеет два существенных недостатка. Во-первых, высокая вероятность возникновения пожарной ситуации (пожары возникают регулярно) и требуется внедрение целого ряда мер по предупреждению возникновения пожара. Во-вторых, продукты горения осаждаются при сушке в материале, повышая зольность. Теоретически существует вероятность взрыва запыленного воздуха при высокихтемпаратурах.
Эти два недостатка не имеют места в схеме с косвенным нагревом, то есть, дымовые газы нагревают воздух через теплообменник. Однако, в такой схеме температура нагретого воздуха из-за ограниченной жаропрочности конструкции теплообменника не может быть выше 200 0С. Практически сложно получить единичную тепловую мощность выше 500 кВт.
Перспективным считается использование пиролизных теплогенераторов. ООО «Промбрикет» успешно провело испытание опытного образца трехходового сушильного агрегата, производительность которого может быть до 1000 кг/час при входной температуре воздуха не более 200 0С.
3. Шнековое прессование
Брикетирование (от франц.- briquette) – это переработка исходных отходов для непрерывного получения продукта (далее рукава) постоянного сечения с одинаковой плотностью. Экономическая выгодность процесса для получения топливных брикетов заключается в том, что в переработку вовлекаются различные отходы растительного происхождения.
Режим брикетирования должен учитывать такие факторы как влажность, фракционный состав, материал отходов. Процесс брикетирования заключается в постепенном сжатии исходного продукта. Высокое давление и повышенная температура в конце прессования приводит к переходу упругих деформаций частиц в пластические, вследствие чего структура материала уплотняется. Создание монолитной структуры обязано выделение смол и их взаимодействие с парами воды и прессуемым материалом.
Конструктивная схема прессов, используемая практически всеми изготовителями, была разработана в Австрии ещѐ в 50-х годах прошлого столетия. Создатели работают над надежностью, технологичностью и удобством эксплуатации.
Наиболее слабым звеном является шнековая насадка, которая на рабочем торце воспринимает большую силу трения и имеет малый ресурс. Австрийская фирма дает ресурс насадки до 40 тонн. Сейчас найдены износостойкие композиции, которые дают ресурс до 80-100 тонн.
4. Резка брикетного рукава
Брикетный рукав, выходящий из экструдера, имеет температуру не менее 200 0С и сравнительно не прочен и поэтому резка производится на охлажденном брикетном рукаве.
Промышленность выпускает автоматические резки брикета. Алгоритм резки реализуется микропроцессором с индикацией количества нарезанных брикетов.
5. Системы автоматики
Для оптимизации процесса сушки необходимо оперативно иметь информацию о влажности исходного продукта и влажности после сушки. Также необходимо знать тепловую мощность воздуха. В промышленности нет влагомера опилок, измеряющего в процессе работы.
Нами найдено решение этой задачи, и внедрение такой системы позволит оператору вести оптимальные процессы, давая при этом максимальную производительность процесса. Из вышеприведенного материала следует, что на выполнение всех технологических операций для производства брикета имеются технические средства, кроме операции измельчения влажной щепы из лесосечных отходов и низкокачественной древесины до фракции 1-3 мм. Поэтому нами поставлена цель обеспечить возможность получения высококалорийного топлива (брикетов) из низкокачественной древесины путем изыскания метода измельчения и конструкции измельчителя щепы из этого сырья и модернизации имеющейся линии для производства брикетов из влажных опилок под осваиваемое производство. Для этого необходимо решить следующие задачи:
1. Проанализировать сырьевую базу для производства топливных брикетов из низкокачественной древесины и лесосечных отходов.
2. Проанализировать известные конструкции измельчителей щепы и изыскать метод измельчения и инструкцию измельчителя влажной низкокачественной щепы до частиц размером 1...3 мм.
3. Адаптировать технические средства, входящие в линию по производству брикета из влажных опилок (сушилку, пресс и др.) для производства брикетов из измельченной влажной низкокачественной цепы.
Исследовать технологию и разработать технологический регламент получения топливных брикетов из вышеуказанного сырья. Актуальность такой работы определяется прежде всего нехваткой дровяной древесины для обеспечения топливом постоянно растущего количества в республике эиергообъектов, работающих на местных видах топлива и введением в топливный баланс невостребованных древесных отходов. Кроме этого, топливные брикеты сегодня по высоким ценам востребованы за рубежом, что может явиться выгодной статьей экспорта для республики.
Однако без специальной технологии и эффективных технических средств ныне невостребованная имеющиеся в больших объемах низкокачественная древесина не могут быть превращены в облагороженное топливо.
Конечным результатом НИР является модернизированная линия для производства топливных брикетов из низкокачественной древесины, а также технологический регламент получения топливных брикетов из низ-кокачественной древесины.
А.Вавилов,
доктор технических наук, профессор,
заведующий кафедрой СДМ БНТУ.
Э.Пересланцев, кандидат технических наук,
заместитель директора ООО «Промбрикет».
Материал подготовлен на основе доклада на международной конференции «Эффективное строительство в Республике Беларусь: современные технологии энергосбережения». г. Минск, февраль 2013 г.
Новости компаний 29.08.2025
Новости компаний 27.08.2025
Новости компаний 26.08.2025
Новости компаний 09.06.2025
Новости компаний 07.04.2025
Аналитика 14.08.2025
Традиционная энергетика 09.06.2025
Технологии 02.07.2021