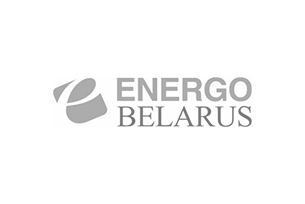
Сравнение отопления тепловым насосом с газом, электричеством и твердым топливом
11.10.2021
Главный энергетик Бобруйского завода тракторных деталей и агрегатов Игорь Леонидович РОЖКОВ делится практическим опытом внедрения транзисторных ВЧ генераторов взамен генераторов машинного и лампового типа.
К концу 2010 - началу 2011 годов на нашем предприятии стали ощущаться проблемы поддержания в рабочем состоянии парка ламповых генераторов ТВЧ. Они использовались в основном для закалки большого перечня деталей.
Ламповые генераторы требуют периодической замены ламп. Проблема в том, что вновь установленные лампы зачастую работали очень короткое время (бывало – меньше месяца) и выходили из строя. Выявить причину таких отказов сложно – то ли это общая изношенность генератора, то ли поставщик лампы недобросовестный и поставил лампу б/у или с хранения.
В итоге годовая стоимость поддержания лампового генератора в рабочем состоянии при замене в год 2-х ламп выливалась в 20 000 $ и выше.
Современной заменой ламповых генераторов, способной работать на тех же частотах, являются транзисторные генераторы. Основными их преимуществами по заявлениям производителей являются надежность и экономичность.
Однако, по опыту, заимствованному на выставках с транзисторными генераторами, мы знали, что есть проблемы перехода на них от ламповых. Производители транзисторных генераторов охотно ведут разговор о решении различных задач и поставках полнокомплектного оборудования под конкретную деталь. Но, когда речь заходит о работе с уже имеющимися индукторами, всплывает множество проблем от чисто механического крепления до согласования электрических параметров. И эти вопросы остаются открытыми без гарантии их решения. Производители предлагают вместе с генераторами покупать и индукторы – но их стоимость при большом перечне деталей может превысить стоимость генератора. Кроме того, производители генераторов редко демонстрируют сложные индукторы высокого инженерного уровня. А у нас такие индукторы почти все.
На нашем предприятии перечень заготовок и, соответственно, индукторов значительный. Например, на одном рабочем месте может обрабатываться до 10 различных заготовок с сильно отличающимися размерами, конфигурациями и типами закаливаемых поверхностей – от наружной и внутренней цилиндрических до зубьев шестерен.
В итоге одновременно с наличием острой необходимости модернизации парка генераторов ТВЧ у нас не было полной уверенности в возможности ее экономичного осуществления без возможных проблем и перебоев.
Для нас речь шла о деталях основной программы, поэтому перебои были недопустимы. В итоге было принято решение объявить закупки не просто транзисторного генератора, а с обеспечением поставщиком работы всего парка индукторов с соблюдением технологических параметров во время закалки (частота, мощность, время) и на обработанном изделии (глубина закалки, твердость).
На таких условиях число претендентов значительно сократилось, но пропорционально возросла их серьезность. Претенденты стали выдвигать встречные пожелания временно предоставить индукторы. По заключенному договору мы получили оборудование, соответствующее решению вышеописанной ситуации.
Таким образом, можно констатировать, что переход от ламповых генераторов на транзисторные возможен без потери функциональности, но требует серьезной проработки, как на стадии составления технического задания, так и на период исполнения договора (предоставление индукторов, приемка с контролем параметров).
Основным достоинством транзисторных генераторов (при условии, что обеспечена надежная работа со всеми деталями) является их экономичность.
КПД транзисторных генераторов от сети до индуктора заявляется не хуже
95 %. КПД ламповых генераторов от сети до индуктора на сегодня известен и многократно проверен – не более 50 %.
Однако это не означает, что транзисторные экономичнее ламповых в 2 раза. Зачастую ряд индукторов хорошо согласован с ламповым генератором, а часть плохо. В итоге бывает, что ламповый генератор на одной и той же мощности греет большую заготовку и в несколько раз меньшую. Это говорит о том, что индуктор большой заготовки хорошо согласован с генератором и хорошо отдает мощность в заготовку, а индуктор маленькой детали – плохо и согласован и отдает мощность.
Транзисторные генераторы имеют автоподстройку под индуктор и обеспечивают cos φ в нагрузке близкий к 1. Поэтому потребление энергии всегда пропорционально закаливаемой площади.
В итоге, благодаря высокому КПД и исключению плохо согласованных индукторов, транзисторные генераторы при сопоставимой производственной программе за сопоставимый период на практике потребляют в среднем в 2,5 – 3 раза меньше электроэнергии.
На нашем предприятии полностью загруженный ламповый генератор 100 кВт был заменен на транзисторный 60 кВт. Кроме того, расход воды только на охлаждение лампового генератора составляет несколько кубических метров в час. Расход воды на индуктор – отдельно.
Транзисторные генераторы благодаря высокому КПД могут быть с воздушным охлаждением. При водяном охлаждении расход незначительный (несколько литров в минуту) и можно считать равным 0, т.к. струю можно пустить сначала на охлаждение генератора, а потом использовать ее на охлаждение индуктора.
Следующим этапом стала замена машинных генераторов ТВЧ.
В этом существует целый ряд проблем. Например, изношенность машинных генераторов и, как следствие - периодическая остановка для ремонта. Ремонт сложный и требует квалифицированных специалистов, возникает проблема приобретения запасных частей.
Второе – изношенность сопряженного оборудования – закалочных трансформаторов и, как следствие - периодическая остановка для ремонта. Процесс ремонта сложный. Это – самостоятельная чистка от накипи и пайка (для пайки требуется квалифицированный пайщик), либо замена дорогих галет. Третье – выход из строя конденсаторов из-за засорения и перегрева.
Четвертое – сложность перенастройки на новые деталь и индуктор.
С учетом нашего опыта было выдвинуто требование обеспечить преемственность работы с имеющимися индукторами.
Основным замечанием претендентов было то, что предлагаемые транзисторные генераторы будут работать на более высоких, чем машинные генераторы частотах. В нашем случае частота машинных генераторов – 8 кГц. Предложенная частота транзисторных генераторов – от 10 кГц.
Такие предложения претендентов у наших технологов вызвали сомнения – будут ли соблюдены требования по глубине закаленного слоя – не будет ли она слишком тонкой?
В процессе проработки вопроса было установлено и подтверждено следующее: более высокие частоты позволяют легко получать закаленные слои той глубины, которая получалась на низких частотах.
Однако задачу подбора соответствующего режима закалки целесообразно возлагать в Техническом задании на Поставщика.
Каков же итог проработки наших методов? Каким представляется экономический эффект?
КПД машинных генераторов по паспорту - 85 %, КПД закалочных трансформаторов – 85%. Общий КПД системы машинный генератор + закалочный трансформатор 85%*85%=72%. Однако машинные генераторы устанавливаются в машинных залах, отдаленных от закалочных постов. Потери в высокочастотной линии от машзала до поста снижают общий КПД системы до 60 - 50% и ниже.
Кроме того, не стоит забывать о потерях холостого хода – когда закалка не производится, а машинный генератор работает.
Транзисторные генераторы устанавливаются рядом с закалочным постом, содержат закалочный трансформатор, работают без холостого хода и имеют КПД от сети до индуктора не хуже 95 %.
В итоге, благодаря высокому КПД, исключению потерь в высокочастотной линии и исключению холостого хода, транзисторные генераторы при сопоставимой производственной программе за сопоставимый период на практике потребляют в среднем в 2,5–3 раза меньше электроэнергии, чем машинные.
На нашем предприятии полностью загруженный машинный генератор 250 кВт был успешно заменен на транзисторный 80 кВт.
Смена индуктора в системе с машинным генератором требует установки на генераторе нужной мощности и подбора емкости конденсаторов, которая производится коммутацией болтовыми соединениями фитилей конденсаторов. Этот процесс занимает минимум 30 минут. Кроме того, плохо зажатые болтовые соединения могут вызвать выход из строя конденсаторов.
В транзисторных генераторах благодаря автоподстройке такой процесс отсутствует. После замены индуктора требуется только выбрать на панели управления соответствующую программу.
Трансформаторы и конденсаторы, установленные в транзисторных генераторах, не имеют водяных каналов, находящихся под потенциалом. Охлаждающая вода на выходе на 2-3 градуса выше, чем на входе. Благодаря этому не происходит образования накипи и засорения. Проблемы перегрева и засорения сопряженного оборудования, присущие машинным генераторам отсутствуют.
Новости компаний 29.08.2025
Новости компаний 27.08.2025
Новости компаний 17.08.2025
Новости компаний 09.06.2025
Новости компаний 07.04.2025
Чтобы оставить комментарий или выставить рейтинг, нужно Войти или Зарегистрироваться