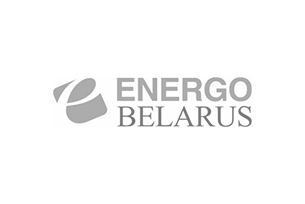
Сравнение отопления тепловым насосом с газом, электричеством и твердым топливом
11.10.2021
Республиканское унитарное предприятие "Белорусский металлургический завод" – предприятие экспортоориентированное. Его продукция поставляется более чем в 50 стран мира, а товарный экспорт превышает 80% от общего объема производства. Завод специализируется на выпуске непрерывнолитой заготовки, сортового проката, бесшовных горячекатаных труб, металлокорда, проволоки различного назначения, фибры.
На «БМЗ» активно ведется инновационная и инвестиционная работа, направленная на создание новых энергоэффективных производств, которые в конечном итоге позволяют снизить себестоимость готового продукта. Этой теме посвятил свой доклад заместитель генерального директора по техническому развитию – главный инженер, ОАО «Белорусский металлургический завод» Сергей Михайлович Борщов, с которым он выступил на симпозиуме в рамках Белорусского промышленного форума-2012.
Основой инновационного развития РУП «БМЗ» на период до 2015 года является проведение технических мероприятий для устранения дисбаланса производственных мощностей и создания условий для увеличения выплавки стали до уровня 3 млн. тонн в год. При этом главным условием является обеспечение полной переработки литой заготовки в готовую товарную продукцию с высокой добавленной стоимостью, создание новых энергоэффективных производств.
Для решения поставленных задач предусматривается модернизация существующих объектов основного и вспомогательного производств, строительство и ввод в эксплуатацию ряда новых объектов. В частности, масштабное перевооружение и модернизация проводятся на Электросталеплавильном, Сортопрокатном, Трубопрокатном и Метизном производствах. Это обеспечивает переход на выпуск продукции принципиально нового качества и потребительских свойств, соответствующей лучшим мировым стандартам и аналогам, снижение удельной энергоемкости, повышение экологической чистоты технологии и производства в целом.
При этом Белорусский металлургический завод, является одним из крупнейших потребителей топливно-энергетических ресурсов (ТЭР) в республике. Например, в текущем году объем ТЭР составит 698 тыс. т.у.т. Структура потребления за последние годы практически неизменна – 75% - электроэнергия, 25% - природный газ.
При проектной мощности 1.250 млн. тонн стали в год, объем выпуска в минувшем году составил 2.607 млн. тонн. Рост производства с одновременным повышением эффективности использования ресурсов – приоритетная задача, поскольку в значительной степени влияет на главную функцию нашей деятельности: максимизацию прибыли, обеспечение рентабельной работы в настоящее время и на перспективу.
Основные направления по снижению энергоемкости производства определены. Это, прежде всего – совершенствование существующих, и внедрение новых энергоэффективных технологий; увеличение глубины переработки стали, выпуск новых, инновационных видов продукции с большей добавленной стоимостью и меньшими энергозатратами; работа по оптимизации использования материалов. В этом случае достигается экономия энергии за счёт снижения уровня отходов производства и эффективного их использования, снижение потребления импортируемого природного газа для нужд технологии и отопления.
В структуре потребления ТЭР завода 65% занимает сталеплавильный комплекс, включающий три сверхмощные 100 тонные дуговые электросталеплавильные печи (ДСП) или около 462 тыс. т.у.т. в год. Это и определяет его развитие, как приоритетное. Снижение энергоемкости на действующем оборудовании, стало возможно, благодаря принятию ряда мер, направленных на достижение наивысших значений производительности, и реализацию ресурсосберегающих технологий.
Наряду с этим были реализованы проекты по модернизации двух дуговых электросталеплавильных печей путем увеличения подачи в рабочее пространство печи кислорода и угольной пыли, как альтернативных источников энергии. Произведена замена печных трансформаторов ДСП - 1, 2, 3 мощностью 75 МВА на новые номинальной мощностью 95 МВА.
Внедрены энергоэффективные токопроводящие консоли на дуговой электросталеплавильной печи, система автоматического регулирования электродов ДСП-3, системы контроля уровня шлака и ряд других технологических новшеств.
Прокатное производство имеет в своем составе 3 разнопрофильных стана – крупносортовой - 850, мелкосортовой - 320 и проволочный стан 150. Процессы прокатки металла полностью автоматизированы. При производстве арматурного проката на непрерывном мелкосортном стане 320 применяется слиттинг-процесс. Опыт успешного использования данной технологии при производстве мелких профилей, показал ее перспективность, для снижения удельного расхода природного газа и электроэнергии.
В комплексе стана 150 применена уникальная методическая пятизонная печь с шагающим подом, что позволяет повысить эффективность нагрева, снизить удельный расход природного газа. За последние 3 года было реализовано более 30 работ по снижению энергоемкости прокатного производства.
Снижение энергоемкости в метизном комплексе лежит в плоскости структурного расширения производства, установки нового и модернизации существующего оборудования. К настоящему времени здесь уже осуществлено внедрение установок компенсации реактивной мощности;
модернизированы канатные машины СД-ТД, FV88, оптимизирована работа станов тонкого волочения, внедрены энергоэффективные технологии производства металлокорда ST и др.
В результате реализации комплекса технических мероприятий, достигнут устойчивый тренд снижения энергоемкости производства. Этот показатель является специальным индикатором, характеризующим уровень эффективности использования энергии в черной металлургии. За период с 2005г по 2011г обеспечено снижение энергоемкости производства с 19,90 ГДж/тыс.USD до 10,14 ГДж/тыс.USD или на 49%. Очевидно, что эффективность использования топливно-энергетических ресурсов значительно повышена.
Для увеличения глубины переработки стали необходимо отметить динамично развивающееся, новое производство бесшовных горячекатанных труб с перспективными объемами 250 тыс. тонн в год. С момента пуска, в 2008 г, освоено 544 профиля труб нефтегазового сортамента, для машиностроения и строительства. Продукция сертифицирована Американским институтом нефти, с правом нанесения монограммы «API», а трубы по DIN EN 10210 признаны победителем профессионального конкурса «Лучший строительный продукт года -2011».
Особое внимание на заводе уделяется вопросу использования тепловых вторичных энергоресурсов (ВЭР), 66% которых занимает тепло газов дуговых сталеплавильных печей. Утилизация такого тепла затруднена, в связи и с неравномерностью его выхода и сложным химическим составом. Тем не менее, в настоящее время реализовано и используется своеобразное техническое решение – водоохлаждаемые контуры газоходов двух сталеплавильных печей. Кроме того, все без исключения нагревательные печи прокатного производства оснащены оборудованием для утилизации и повторного использования тепловой энергии. В2011г доля ВЭР в балансе котельно-печного топлива достигла 20,6%, а в балансе тепловой энергии, выработанной собственными энергоисточниками – 75%.
Два года назад в систему менеджмента завода включен раздел СУЭП – Система управления энергопотреблением, разработанная в соответствии с требованиями национального (СТБ 1777-2010) и Европейского (EN:160001) стандартов. Основа подхода выстроена на четком документировании и управлении взаимосвязанными процессами, которые существенным образом влияют на эффективность энергопотребления. Благодаря развитой автоматизированной системе технического учета энергоресурсов (АСТУЭ), производится мониторинг потребления ТЭР в режиме реального времени, а также ежедневный оперативный учёт, с подведением итога и выполнением корректировки, при необходимости. Такая форма контроля, позволяет эффективно управлять энергоёмкостью с использованием организационных мер и системно уточнять технические мероприятия.
Система учета энергоресурсов с помощью локальной компьютерной сети связана и адаптирована под использование, совместно с системой управления технологическим процессом. Создан реальный научно-технический ресурс для снижения издержек, и, как следствие – получения дополнительных доходов.
Несмотря на постоянный рост стоимости энергоресурсов, принятыми мерами удается удерживать долю ТЭР в себестоимости продукции на уровне не выше 20%, что характеризует существующий уровень использования энергии, как соответствующий лучшим мировым аналогам. За 2011г данный показатель составил 19,2%. Результат достигнут благодаря инвестициям в реконструкцию, модернизацию и техническое перевооружение. Объем вложенных средств только в 2011 году составил более 437.2 млрд. руб. Финансирование проектов осуществляется за счет собственных средств.
/////////////
Новости компаний 24.06.2025
Новости компаний 20.06.2025
Новости компаний 17.06.2025
Новости компаний 30.06.2022
Технологии 17.06.2025
Чтобы оставить комментарий или выставить рейтинг, нужно Войти или Зарегистрироваться